Keep it clean! Often easier said than done
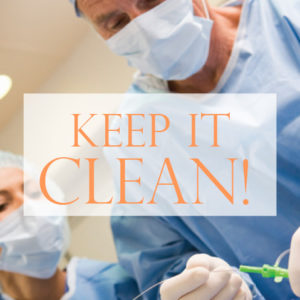
Recently, efforts to improve disinfection and sterilization in healthcare facilities were spurred by Medicare reimbursement cuts to hospitals along with new guidelines from the U.S. Centers for Disease Control and Prevention (CDC). Despite the renewed focus, in 2011 there were still 721,800 cases of Healthcare-Acquired Infections (HAIs) with 75,000 deaths.
Lots of work remains to be done to reach disinfection and sterilization standards
As it stands, only 30 percent to 38 percent of U.S. hospitals are in full compliance with the CDC’s current infection control guidelines. 100 percent compliance is a reasonable goal, but there remains a sizeable gap to close. Getting there starts with the creation of reliable, affordable and easily obtainable antimicrobial products so healthcare providers can better-prevent device-associated infections.
Antimicrobial coatings vs. homogenous antimicrobial materials
While antimicrobial coatings may be an attractive option for some applications, they have their shortcomings. Coatings are often limited in efficacy to the surface of the device, not to mention the uniformity of their application must be closely monitored during a secondary, and often costly, manufacturing process. On the other hand, homogenous antimicrobial materials are effective immediately out of the mold or die and retain their efficacy even when damaged or abraded.
Parker has overcome many of the polymer processing limitations that have traditionally plagued antimicrobial compounds. Our elastomers with select antimicrobials additives have shown excellent antimicrobial efficacy (99.99 percent) and biocompatibility while maintaining virtually all mechanical properties and processing capabilities.
What to consider when designing medical devices
Device manufacturers are encouraged to be as specific as possible when providing their initial design parameters. Antimicrobial polymers are available in several HAI-resistant applications, including vascular access, fluid management, instrument housing, airway management, laparoscopy, wound dressings, Class I, II, and III medical devices and more. Beyond the functionality requirements of a given device, consideration should be put into how damp the end-use environment will be, how long a device will be used, and what color/transparency/translucency requirements a device may have. Discussing as much as possible up-front allows for a quicker development stage and better, more cost-effective results overall…
Read the full article at blog.parker.com
TEK’s ISO Class 7 Clean Room was added to our Randolph warehouse in the fall of 2014. Our clean room allows us to support customers better than ever before.
The new clean room supports our abilities to perform sterile assemblies, manifolds and packaging in house. Our product offering will include single use sterile filters, bags, quick disconnects, hose barb connections, over-mold junctions and manifolds, valving, tube, hose and so much more.
To learn more about our clean room capabilities contact our team.